Interview with Matthew Costello, Corporate Vice President, Global Operations for Sony Ericsson |
Matthew Costello is Corporate Vice President, Global Operations for Sony Ericsson Mobile Communications, a global leading provider of mobile handsets, accessories and content and services. In this capacity, Matthew reports to Sony Ericsson's CEO and sits on the company's Executive Committee. Prior to serving as Global Operations Head, Matthew served as Sony Ericsson's Chief Procurement Officer and Head of Corporate Strategy, Transformation and Restructuring.
Matthew joined Sony Ericsson in early 2007 as Senior Vice President, Transformation and Programmes, having served as an external consultant in leading the redesign and implementation of Sony Ericsson's global Supply Chain and Sourcing organization and capability. This development initiative helped to earn Sony Ericsson a spot on Advanced Manufacturing Research's prestigious Global "Top 25 Best Supply Chains" for 2008 and 2009.
Prior to joining Sony Ericsson in 2007, Matthew served as Vice-President, Global Supply Chain for BearingPoint, Inc, a NYSE listed leading global management and technology consultancy. Matthew joined BearingPoint from Andersen in 2002 upon its collapse. During the course of his consultancy career, Matthew specialized in Supply Chain and Operational transformation and restructuring projects, leading the definition of new strategies and linking these to processes, tools, systems and people to enable concepts to become reality. Matthew focused on retail and fast moving consumer goods for several years prior to transitioning to high-tech related operational transformations in early 2000.
Prior to joining Andersen, Matthew received a Bachelors with High Honors in Economics and Government from Duquesne University and a Diploma in International Economics from Katholieke Universiteit Leuven, Belgium. Matthew has three children, a Swedish wife and resides in Stockholm with offices in London.
How important is supply chain management to Sony Ericsson's overall business strategy?
Supply Chain/Operations is one of the four cornerstones of the overall company strategy.
What primary areas of focus (or key initiatives) should Sony Ericsson be looking at for Supply Chain Management?
Sony Ericsson has developed, according to AMR, into one of the top 25 global supply chains globally, over the past 4 years. This success has been based upon a number of key factors:
- A fully integrated, end to end planning setup
- A tightly integrated process for managing product development across all product phases
- A robust build to order manufacturing model
- A balanced internal and external asset approach (in manufacturing)
- A leading approach to sustainability
- CSR and a global way of integrating suppliers into the value chain
The next step in our development focuses upon improving lead times and flexibility to our customers around the globe while managing risks along the entire supply chain, creating more "clustered" capabilities within our supply chain to take more advantage of scale. Further, we will take our integrated approach to development to the next level focused upon more advanced planning while limiting risks across the value chain.
How has outsourcing enabled Sony Ericsson to be successful with these initiatives?
We have a balanced approach to outsourcing - we have clearly articulated the role that outsourcing partners play in all aspects of our value chain and build internal capabilities and, simultaneously, capabilities to effectively manage our "outsourced" partners along the lines of this strategy. In this sense, any partner - EMS; ODM, component supplier, logistics provider - is always a fully integrated component of our overall strategy and approach.
How is Sony Ericsson addressing the market's increasing focus on 'green' supply chains and reducing a company's carbon footprint?
Sony Ericsson is widely recognized as a leader in sustainability and has been working with CSR and carbon emissions policies for several years. We imbed Sustainability considerations in every aspect of our decision making framework - hence, we have extended our QCD framework (Quality, Cost and Delivery) to include sustainability to form QCDS.
Over the past few years, we have extended our sustainability capability set into a line of products known as GreenHeart. We are constantly working to reduce our carbon footprint and are now working on a forward configuration approach that will enable us to reduce our reliance on air based transports.
What is the key Supply Chain Management priority for the coming 2-3 years for Sony Ericsson?
Our supply chain is reliable and very cash efficient. Our next step is to evolve our supply chain to a model which maintains our risk profile while enabling reductions in lead times to customers while increasing our offered "flexibility" within the frozen horizon.
What is the key Supply Chain Management priority for the coming 5-10 years for Sony Ericsson?
Our industry is extraordinarily dynamic and hence, our planning cycle is 3 years. I would suggest, however, that our internal and our partners' reliance upon Asia - and China more specifically - will need to be carefully monitored going forward. Hence, our footprint is our priority on a 5 year basis.
What are the biggest INTERNAL challenges for manufacturers to achieve supply chain excellence?
In a highly volatile, exceptionally high volume consumer industry such as mobile phones, there are two predominant internal challenges - forecasting effectively and ensuring quality in all dimensions.
What are the biggest EXTERNAL challenges in achieving supply chain excellence?
Market volatility is an internal and external threat. As such, securing flexibility at the right cost given our Asia operational footprint is our largest challenge. Several operational challenges also exist, given forecasting considerations, to increase flexibility while managing risk.
What are the supply chain challenges to which Sony Ericsson SHOULD be paying more attention?
Our current supply chain challenges include short term flexibility and shortened lead times given market dynamics.
Who is responsible for planning your company's business continuity when facing natural disasters, major disruptions or other geopolitical issues?
Our Corporate Operations department is responsible for planning our response to natural disasters, major disruptions and geopolitical issues.
How do you grade Sony Ericsson's supply chain overall performance in client satisfaction?
We are a leader in satisfying Operator-customers. We are slightly less competitive in distributor oriented markets.
During this economic downturn, how do you keep your entire organization motivated?
Great question. We have conducted significant organizational restructuring on a global basis and have faced difficult times internally. Ultimately, our staff realizes that the consumer dynamic and technical complexity makes this a truly unique and intriguing industry. On top of this, we have attempted to ensure continuous forward development of our supply chain to motivate our colleagues.
What are the key factors to ensure a successful Contract Manufacturer (CM) relationship?
It is extremely important to drive relations with EMS in the same fashion as we work with internal factories. We drive process development in the same way towards internal and external partners. We do not treat CM partners at "arms length."
How important is trust in the Sony Ericsson/CM relationships?
Trust in our CM's is critical to our company.
How do you prepare for the upturn now that the economy is showing improvement?
We are extending our risk profile on a product / customer / market basis to prepare for potential upside requests.
When do the fuel cost / dollar exchange and / or geopolitical factors make insourcing a viable option?
This balance is a constant on our agenda.
What are your thoughts regarding globalization?
Our industry is extraordinarily global in setup and reach. Hence, it is a prerequisite in both our footprint, resource base and mindset. We have operations centers in California, Atlanta, Sao Paolo, Sweden, Munich, Beijing, Taipei and Tokyo.
What attracted you to supply chain management?
I was attracted to supply chain management because Operations is "strategic", "analytical" and "hands on" all at the same time. It also interfaces with every aspect of the Sony Ericsson ecosystem. It is an ideal and fascinating role and journey.
What are the main skills and personal attributes that have helped you reach your current position?
Having "grown up" in consulting, I learned solid analytics; relation-building and thorough execution combined with keen "people" understanding and team building. These attributes - combined with a high integrity in my views and actions - have served me well.
What would you say is the most rewarding experience you've had in your career?
When I first joined Sony Ericsson, I was positioned in a role of "Corporate Transformation." After almost 15 years in consulting, I expected it to be easier to implement "change" as an internal resource. What I realized is that change is extraordinarily challenging no matter the context and, hence, it is the power of the ideas and tenacity in the approach which makes the difference.
What have you learned as Corporate Vice President, Global Operations that has surprised you or changed the way you do business?
The power of long term relations is absolutely fundamental in designing and managing global operations capabilities.
Who do you rely on for advice?
I have several mentors with senior executive experience that I frequently seek for counsel and advice
How do you balance your work life with your personal life?
The true challenge in my life. I have an extraordinary and understanding wife.
Turbulent times can be the best time to implement changes. However, companies tend to paralyze due to uncertainty in the market or their human capital. What is your advice to maximize the opportunities to implement changes during tough times?
I thrive in it. My consulting background and the issues we have faced over the last 2 years in Sony Ericsson
have allowed me to understand that challenging times bring unique opportunities to change and develop
rapidly both in terms of capability and cultural transformation. |
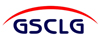 |
|
May 2010 |
|
|
|
|
|
|