Five Mistakes Companies Make When Trying to Effectively Manage Supply Chain Risk |
By Bindiya Vakil, President & CEO, Resilinc and Hannah Kain, President & CEO, ALOM
Supply chain resiliency is the ability of a company to recover from a disruption, as determined by the time and cost of recovery. It is a function of everyday decisions such as which suppliers the company sources from, how the volume is split between sources, where manufacturing facilities are located, how much inventory and second sourcing has been put in place, etc.
Yet, there are many factors eroding the resiliency of today’s supply chains. Over the last 15 years companies have adopted lean and just-in-time (JIT) practices as well as build-to-order type capabilities in a big way. This means that global supply chains are overly optimized to operational parameters such as lead times, and often have low levels of buffers that would help to withstand disruptions. In addition, business metrics focus heavily on cost reduction and inventory turns – short-term incentives tied to these metrics further result in decisions at every level, which further erodes resiliency in the supply chain. A growing focus on cost, inventory reduction and lean in the backdrop of a globally dispersed and multi-tiered supply chain has resulted in small disruptions causing a big impact.
Traditional supply chain management practices leave vast gaps in resiliency because supply chain risk management is fundamentally different from everyday operations management. When companies fail to recognize and appreciate these differences, they fail to manage risk effectively. Outlined below are five mistakes commonly made in managing supply chain risk and ways in which companies can improve the resiliency of their supply chain.
1. Quantifying Everything by Spend and Not by Impact
Supply chain functions are typically prioritized by spend. When asked to name critical suppliers or parts, most supply chain professionals will identify the top 20 percent of parts or suppliers that constitute 80 percent of the total spend. Resource, time and budget allocations are also organized by spend, and it has worked well – until now. Over the past 15 years, the global dynamics have changed. With the ease and cost to setup offshore operations and outsource parts of the supply chain to sub-contractors, companies now have multi-layered supply chains spread across the globe. Often, disruptions occur in the long tail – the 80 percent of suppliers representing 20 percent of the spend – especially if the low spend category relies mostly on single-sourced or custom material.
In order to ship a product, every single part needs to be present – this is the fundamental challenge for supply chain practitioners. The biggest mistake in optimizing everything based on cost/spend is that the overall impact to business is ignored. Custom paint, connectors, power supplies and other low spend items and even some kinds of labels with no alternate source can become single points of failure in the supply chain. After all, we can’t ship a car without paint, or a laptop missing a connector or button. A hybrid approach looks at the revenue impact of losing a particular part or supplier, and considers single-sourced, custom dependency on low spend suppliers.
2. Not Getting to the Root Cause of the Problem – Visibility
The fundamental challenge with risk management today is the lack of visibility across global supply chain dependencies. The answer to “What is my true supply chain?” is incomplete at best. There is often no visibility into where parts come from or who is building them. Are dual-sourced parts truly dual-sourced or are there single-sourced dependencies one or two levels up the supply chain?
While there is widespread acknowledgement of the problem, very few have done what is needed to gain visibility and enable control. Once these questions have been effectively answered and the impact of losing a part, site or source has been determined, a prioritization strategy needs to be formulated to help identify high impact areas of the supply chain that need immediate mitigation. This will help deal with not only large catastrophic events, but also many smaller location-related disruptions that supply chain practitioners encounter on an ongoing basis.
3. Consistently Putting Risk Management Under Immediate, Short-Term Priorities
The world of supply chain management is highly dynamic. Organizations must constantly address operational challenges such as shortages, demand increases, excess, supplier issues, delivery delays and quality problems, while often being under intense budget constraints. As a result, organizations often must flit from one issue to another; always reacting or scrambling to address problems. Key decision makers lack the time to step back and assess the supply chain proactively or take efforts to gain greater visibility and control.
Rewards and incentives are also tied to achieving short-term goals around cost savings, inventory turns, time to market, etc. This incentive misalignment causes indiscriminate inventory reduction and a push to source or manufacture in areas with high supply concentration. Since proactive supply chain risk management is the one activity that is at odds with targets, incentives and rewards, it is the one activity that is easier to deprioritize. In order to ensure that this doesn’t happen, risk management/mitigation efforts need to be tied to metrics and incorporated into processes and reviews that are supported with regular reinforcement and incentives from the top level down.
4. No One Person is Accountable for Risk Management
A 2008 Procurement Strategy Council report indicated that the vast majority of CxOs hold the Chief Procurement Officer (CPO) accountable for response to supply chain disruptions 1. However, it is not at all clear who the CPO holds accountable in his/her organization. Most companies do not have this responsibility assigned to a person or group within the supply chain or procurement organization – i.e. someone who can take leadership at an operational level. This means, when there is a crisis, there is a large amount of confusion and lack of coordination as extraordinary response actions fall outside the normal scope of activities.
Every crisis needs a leader for effective response coordination and recovery – often putting the supply chain leadership in the spotlight. A May 2011 study by W P Carey revealed that leadership is as critical as effective systems for a crisis response2. A strong leader, appointed in advance, trained and equipped with information, tools and a solid crisis response infrastructure can help the CPO appear to be in control, rather than at the mercy of the event.
5. Subconsciously Endorsing the Diving Catch Approach
A crisis, even a small one with low to no impact, is an opportunity to learn and take proactive steps for risk management. However, this critical point is not sufficiently appreciated. Often we think we got lucky when we are not impacted or are able to recover quickly. A crisis war room is also perceived to be the place where employees get exposure to top executives, only adding to the resistance to dedicate resources to proactive risk management. If product gets to the customer by paying 20 times premium and 10 times freight expedites, the execution team appears to have “saved the day.” While necessary in extraordinary times, this type of “diving catch” approach for every situation has a dramatic impact on profitability. A post-crisis assessment would reveal the true cost to the business of such an approach.
A post-crisis assessment is very important in gaining insight into what went wrong and where investment and attention is needed to ensure an organization is better informed, more in control, more coordinated and less impacted the next time. Smaller disruptions should be perceived as drills and training for when a larger event strikes. Rewards should be in place for crisis aversion rather than crisis response. This is the best way to ensure that proactive risk management becomes embedded in an organization’s culture.
Conclusion
Supply chain risk management has to be thought of as a strategic investment and viewed in the context of long-term gains. To be effective, it needs a fundamentally different approach from traditional supply chain management. As long as these differences go under-appreciated, companies will not focus efforts where they are truly required, nor will they solve the visibility-related issues that are at the root cause of the problem. In the end, companies are not empowering or encouraging people to make resilient choices proactively, which means they will be in a reactive mode in every disruption – scrambling to catch up.
Given the widespread globalization of the supply chain and the extreme impact of disruptions on corporate results, supply chain risk management is on the fast track to become a corporate governance issue requiring the attention of not only the CPO, but also the CEO and eventually the Board. The reality of the new globalized world is that we are going to face disruptions from one corner of the globe after another. It is time for companies to invest in the necessary tools, processes and leaders to ensure they have a well-oiled and trained machine for swift, coordinated crisis response every time they are faced with a supply chain disruption.
1. “Defense of the Enterprise: 2008 Supply Risk Management Benchmarking Survey.” 2008. Procurement Strategy Council. Online: https://psc.executiveboard.com
2. “Most Valuable Asset During Supply Chain Disruptions: Strong Leader or Great System?” May, 2011. W. P. Carey & Co. LLC. Online: www.wpcarey.com
|
About Resilinc |
Resilinc offers an end to end cloud-based solution for proactive supply chain risk management deployed with large and mid-sized High Tech companies. Delivered on the Force.com platform, their highly scalable supply chain mapping solution helps capture global locations where parts originate and quantify revenue impact of losing a supplier, part, site or region as well as risk scores. Their crisis solution involves crisis preparedness tools, disruption monitoring and response capabilities, as well as enterprise social networking to capture the collaborative elements of a truly effective risk management platform. |
|
|
About ALOM |
ALOM is a Fremont, California-based supply chain management provider that has been ISO-certified since 1998. Services include materials and inventory management, logistics, assembly, light manufacturing, fulfillment, and reverse logistics from 14 locations across North America, Asia and Europe. More information is available at www.alom.com. |
|
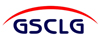 |
|
November 2011 |
|
|
|
|
|
|